在材料制備、實驗室分析及工業生產中,熔片機是一種重要的設備,用于將樣品熔融并制成均勻的片狀材料。然而,在實際操作中,熔片裂片是一個常見問題,不僅影響樣品質量,還可能導致設備損壞和生產效率下降。本文將深入分析熔片裂片的原因,并提供相應的解決方案。
一、熔片裂片的主要原因
1.溫度控制不當
①溫度過高:過高的熔融溫度可能導致樣品過度熔化,冷卻時因熱應力過大而產生裂紋。
②溫度過低:溫度不足會使樣品熔融不充分,內部應力分布不均,冷卻后易出現裂片。
2.冷卻速率過快:快速冷卻會使樣品表面與內部產生較大的溫度梯度,導致熱應力集中,從而引發裂片。例如,在金屬熔片過程中,冷卻速率過快是裂片的常見原因之一。
3.樣品成分不均勻:樣品中雜質或成分分布不均會導致熔融過程中局部應力集中,冷卻后易產生裂紋。例如,在玻璃熔片過程中,未充分混合的原料可能導致裂片。
4.模具設計不合理
①模具材質不當:模具的熱膨脹系數與樣品不匹配,冷卻時可能因收縮不均導致裂片。
②模具結構缺陷:模具表面粗糙或存在尖銳邊緣,可能使樣品在冷卻過程中產生應力集中。
5.操作工藝問題
①熔融時間不足:樣品未全部熔融,內部存在未熔化的顆粒,冷卻后易產生裂紋。
②壓力控制不當:熔融過程中壓力過大或過小,均可能導致樣品內部應力分布不均。
二、解決熔片裂片的方案
1.優化溫度控制:根據樣品特性設定合適的熔融溫度,避免溫度過高或過低。使用高精度溫控系統,確保熔融過程中溫度穩定。
2.調整冷卻速率:采用梯度冷卻或緩慢冷卻方式,減少樣品表面與內部的溫度梯度。在冷卻過程中使用保溫材料,延緩冷卻速率。
3.改善樣品均勻性:在熔融前對樣品進行充分混合,確保成分分布均勻。使用高純度原料,減少雜質對熔融過程的影響。
4.改進模具設計:選擇與樣品熱膨脹系數匹配的模具材質,減少冷卻時的收縮差異。優化模具結構,確保表面光滑、無尖銳邊緣,減少應力集中。
5.規范操作工藝:確保樣品全部熔融,避免未熔化顆粒的存在。根據樣品特性調整熔融壓力,確保內部應力分布均勻。
三、預防熔片裂片的措施
1.定期維護設備:檢查加熱元件、溫控系統和模具狀態,確保設備運行正常。定期清潔設備,避免雜質積累影響熔融效果。
2.加強操作培訓:對操作人員進行專業培訓,確保其掌握正確的操作方法和工藝參數。建立標準操作規程,減少人為操作失誤。
3.進行工藝驗證:在正式生產前進行小批量試驗,驗證工藝參數的合理性。根據試驗結果優化工藝,確保生產過程的穩定性。
四、未來發展趨勢
隨著材料科學和制造技術的進步,熔片機正朝著智能化、自動化方向發展。例如,通過集成傳感器和AI算法,實時監測熔融過程中的溫度、壓力等參數,自動調整工藝條件,減少裂片的發生。
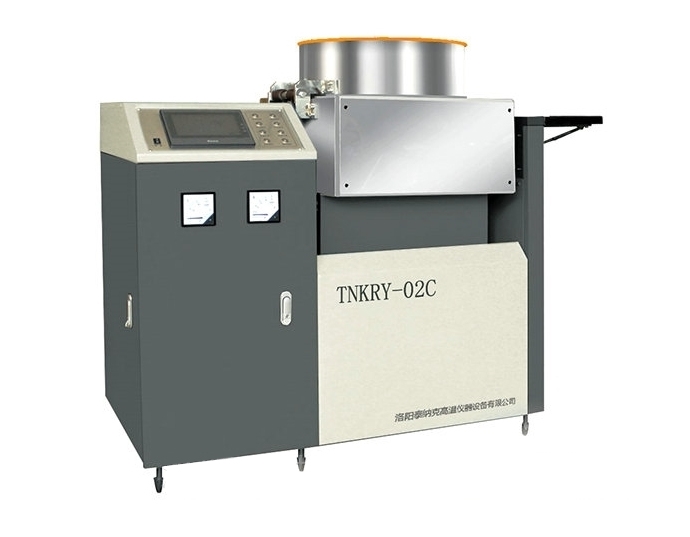
五、結語
熔片機熔片裂片是一個復雜的問題,涉及溫度控制、冷卻速率、樣品成分、模具設計及操作工藝等多個因素。通過分析原因并采取針對性的解決方案,可以有效減少裂片的發生,提高樣品質量和生產效率。